Solid Edge - How to build a study with many connected parts
Introduction
When there are many parts in a study, the amount of connectors (created automatically or manually) can be overwhelming. It is important to remain in control of those connectors as their quantity increases. Otherwise, it will be a difficult task to find the source of the problem when a fatal error occurs during solving.
A recommended method for medium size assemblies
The user of Solid Edge can include only a subset of the parts that will eventually need to be analyzed. This way, a limited amount of connectors will have to be created. The workflow is to modify the boundary conditions to accommodate this partial study (add temporary load or constraint) and solve to verify that the connectors play their role and keep the studied parts connected. Then, the user can modify the definition of the study to add more parts or start from a copy of the study to keep a backup of each step. Each following steps, necessary to build the full study, will require the addition of new connectors and modification of the boundary conditions.
A recommended method for large size assemblies (with thin walled parts)
The user of Solid Edge should use mid-surfaces (psm) or other type of surfaces when analysing thin-walled parts. In addition to this, the user has the option to connect surfaces in contact to create one or several associated bodies for the analysis. This will remove the need for connectors as the nodes merge at the intersections. This approach needs to be considered seriously when hundreds of parts are being analyzed.
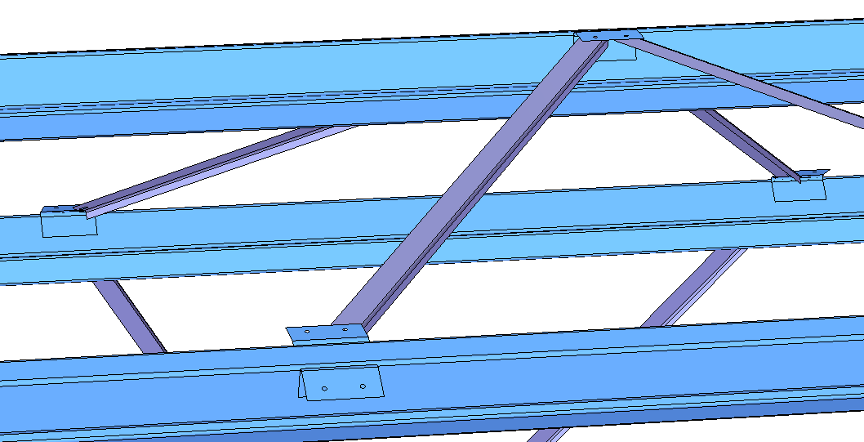
Conclusion
With these workflows, the Solid Edge user who wants to build a complex analysis can confidently and progressively add all the required simulation features to run a full study. The capacity to verify a subset of connectors and, afterwards, move on confidently to the next group of connectors can be a huge time saver when dealing with large assemblies.
June 4, 2024